Exploring the Power of Claw Drills in Chain Applications
When it comes to enhancing project efficiencies across numerous sectors, Claw Drills have emerged as game changers. From construction to automotive repairs and industrial manufacturing processes, these innovative tools are designed to meet high-demands with ease.
Understanding Claw Drills
Claw Drills are advanced drilling tools specifically engineered to handle rigorous chain applications. What sets them apart from standard drills is their robust build and specialized design tailored for precision and speed.
- Definition and Primary Uses: Crafted to drill through dense materials seamlessly, they cater primarily to industries where chain mechanisms play a crucial role. Whether it's cutting through heavy metal or repeat tasks requiring unerring accuracy, Claw Drills excel effortlessly.
- Key Features: Enhanced torque, precise control, ergonomic grip, and extended durability differentiate Claw Drills from conventional options. These attributes ensure minimal downtime while optimizing productivity.
Advantages of Using Claw Drills
The power-packed performance of Claw Drills offers several advantages that translate directly into enhanced operational efficiency.
- Enhanced Drilling Speed: Engineered for swift penetration, reducing time spent on every task significantly.
- Precision and Accuracy: Ideal for meticulous chain applications where exactitude is paramount.
- Increased Durability: Built to withstand intense use without compromising performance, ensuring long-term reliability.
Real-World Applications
Versatility defines Claw Drills, making them indispensable tools in varied sectors.
- Construction Industry Usage: Speeds up drilling during foundation laying, structural reinforcements, and other critical areas.
- Automotive Repairs and Maintenance: Facilitates quick yet precise fixes, improving service turnaround times.
- Industrial Manufacturing Processes: Reduces assembly line downtimes and boosts overall production efficacy.
Case Studies: Transformative Impact
Case Study 1: Reducing Assembly Line Downtime in a Manufacturing Plant
Initial Challenges: Frequent halts due to inefficient drilling tools resulted in accumulated delays.
Implementation of Claw Drills: Introduction led to an immediate improvement in uptime, facilitating seamless operation.
Measurable Improvements and Outcomes: Significant reduction in downtime; notable increase in daily output rates.
Case Study 2: Streamlining Construction Workflows on a Major Project
Project Overview: A large-scale infrastructure development faced schedule pressures due to labor-intensive drilling requirements.
Role of Claw Drills: Employed for key drilling tasks, drastically speeding up workflows.
Feedback from Project Managers and Workers: High praise for ease of use and remarkable impact on meeting deadlines.
User Testimonials
Professionals across industries vouch for the effectiveness of Claw Drills.
- Ease of Use: Ergonomically designed handles facilitate comfort and reduce fatigue even after prolonged usage.
- Enhanced Timelines: Predictable performance allows better planning and adherence to project schedules.
- Durability and Maintenance Savings: Reduced need for frequent replacements lowers costs over time.
Tips for Maximizing Efficiency with Claw Drills
- Proper Handling and Safety Precautions: Always adhere to safety guidelines to prevent mishaps.
- Maintenance Best Practices: Regularly clean and inspect your tool to extend its operational life.
- Selecting the Right Model: Choose the correct Claw Drill model based on specific task requirements for optimum results.
Comparing Claw Drills to Conventional Drills
- Performance Metrics: Higher RPMs and consistent torque set Claw Drills ahead.
- Cost-Benefit Analysis: While initially pricier, long-term savings and boosted productivity justify the investment.
- User Experiences: Favorable feedback highlights significant differences in handling and outcomes compared to traditional drills.
Future Innovations and Trends
With technology evolving at breakneck speeds, Claw Drills continue to integrate emerging innovations.
- Emerging Technologies: Expect smarter sensors, IoT integration, and AI-assisted capabilities in next-gen models.
- Evolving Designs: Refinements aimed at reduced weight and increased compactness will further user convenience.
- Potential New Applications: Expanding utility beyond current domains into new industries facing intricate drilling challenges.
Final Thoughts from Industry Experts
Experts unanimously recognize the transformative potential of Claw Drills in modern workplaces.
"For professionals deliberating investing in Claw Drills, the value proposition lies not just in immediate benefits but also sustained gains in efficiency, quality, and safety."
Continued advancements keep pushing boundaries, cementing Claw Drills as indispensable assets in both existing and future projects.
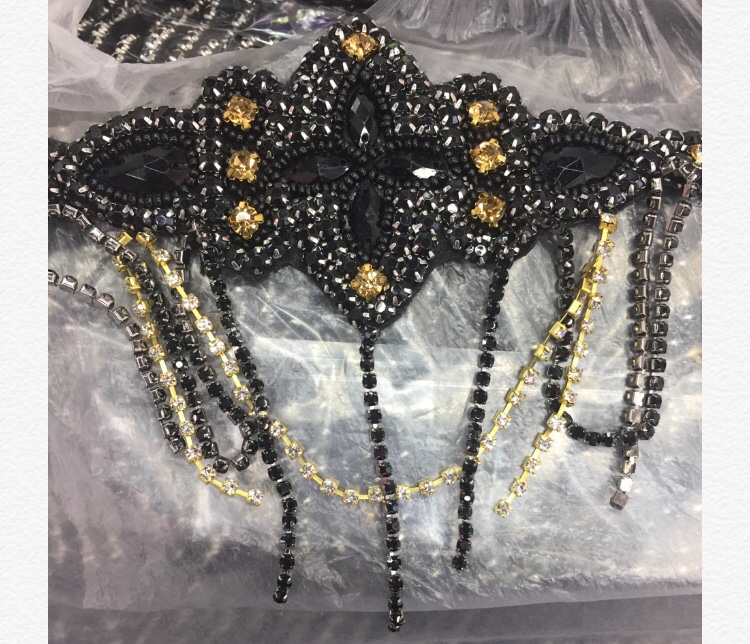